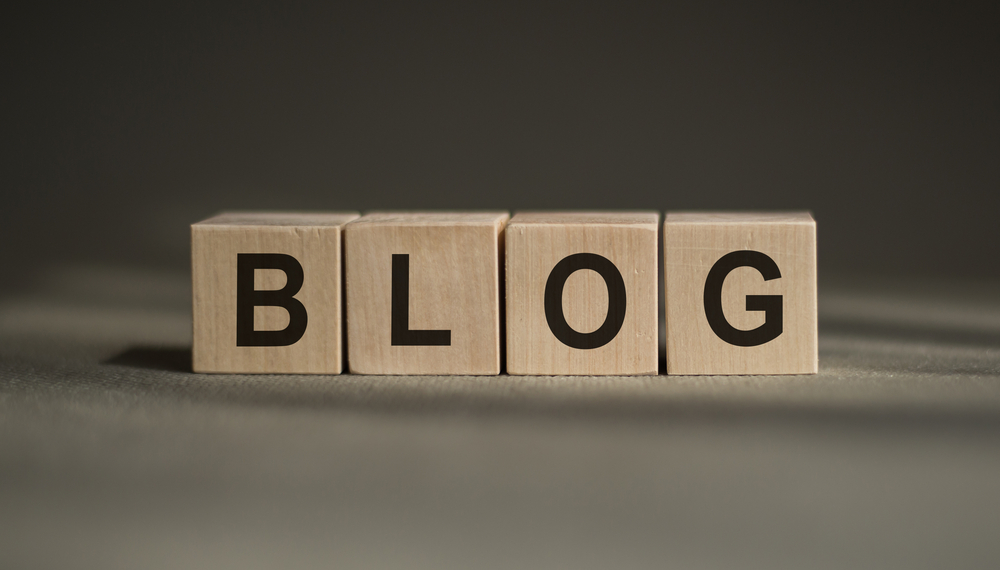
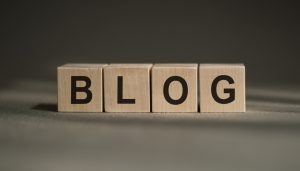
Temporary Site Infrastructure: What You Actually Need for Remote Projects
Related Articles Article Download PDF version of this article Download Share Setting up a functional and safe remote project site in Saudi Arabia involves more
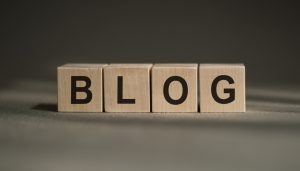
What to Consider When Choosing a Power Generator for a Job Site in Saudi Arabia
Related Articles Article Download PDF version of this article Download Share Selecting the right power generator is one of the most critical decisions for any
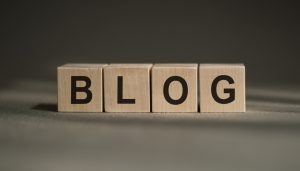
Why Modular Buildings Are Transforming Worksites in Saudi Arabia
Related Articles Article Download PDF version of this article Download Share In today’s high-pressure project environments, companies need site solutions that are fast, reliable, and
Why Modular Buildings Are Transforming Worksites in Saudi Arabia
In today’s high-pressure project environments, companies need site solutions that are fast, reliable, and adaptable. That’s why modular buildings are quickly becoming the preferred choice for temporary infrastructure across construction, oil & gas, logistics, and public sector projects in Saudi Arabia.
Unlike traditional construction, modular buildings are pre-engineered, allowing them to be deployed rapidly and scaled as needed. From mobile offices and rest areas to restrooms, security cabins, and worker accommodations, modular structures offer comfort, functionality, and speed — all in one package. Their plug-and-play design helps reduce setup time and labor costs, which is especially important in remote or high-traffic worksites.
What makes modular buildings particularly suited to Saudi Arabia is their durability and customizability. Leading providers now offer units built from fire-retardant steel, insulated with polyurethane foam for thermal efficiency, and equipped with certified electrical systems. Features like forklift pockets and skid-mounted bases ensure safe and easy transport to desert sites, urban zones, or offshore rigs.
Scalability is another major advantage. With built-in expansion joints and standardized dimensions, multiple units can be connected seamlessly to create larger office complexes or full site camps. This allows teams to adjust infrastructure as the project evolves — without starting from scratch.
As demand for flexible infrastructure grows across the Kingdom, modular buildings are proving to be more than a temporary fix. They’re becoming an essential part of how modern worksites operate — combining speed, safety, and sustainability with the adaptability today’s industries need.